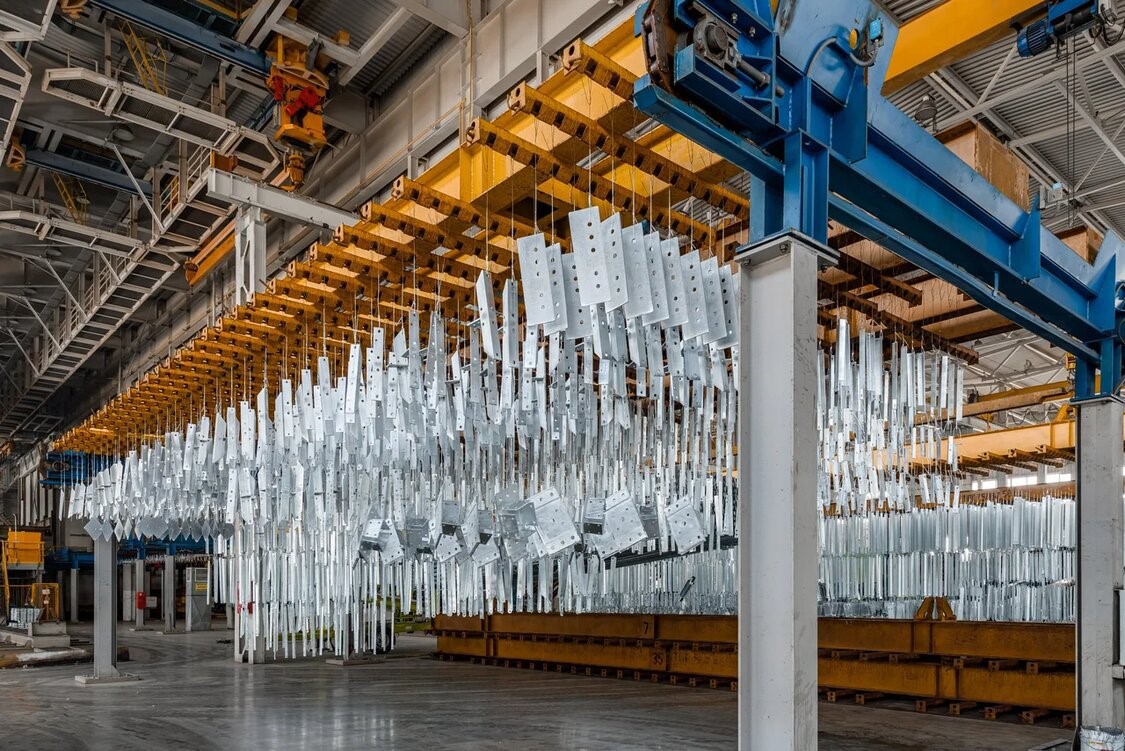
От истоков до ведущего предприятия
Свердловский завод металлоконструкций, а ныне UMECON (Уральский завод металлоконструкций), был основан в 1951 году. 69-летняя история завода — это постоянное расширение производственных мощностей и освоение более эффективных технологий производства, включая автоматизацию процессов, а также улучшение условий труда сотрудников.
Сегодня UMECON входит в топ-3 крупнейших заводов России и стран СНГ, производящих металлоконструкции и опоры линий электропередачи. Обладая огромным опытом и мощной научно-производственной базой, завод изготавливает до 60 тысяч тонн металлоконструкций в год.
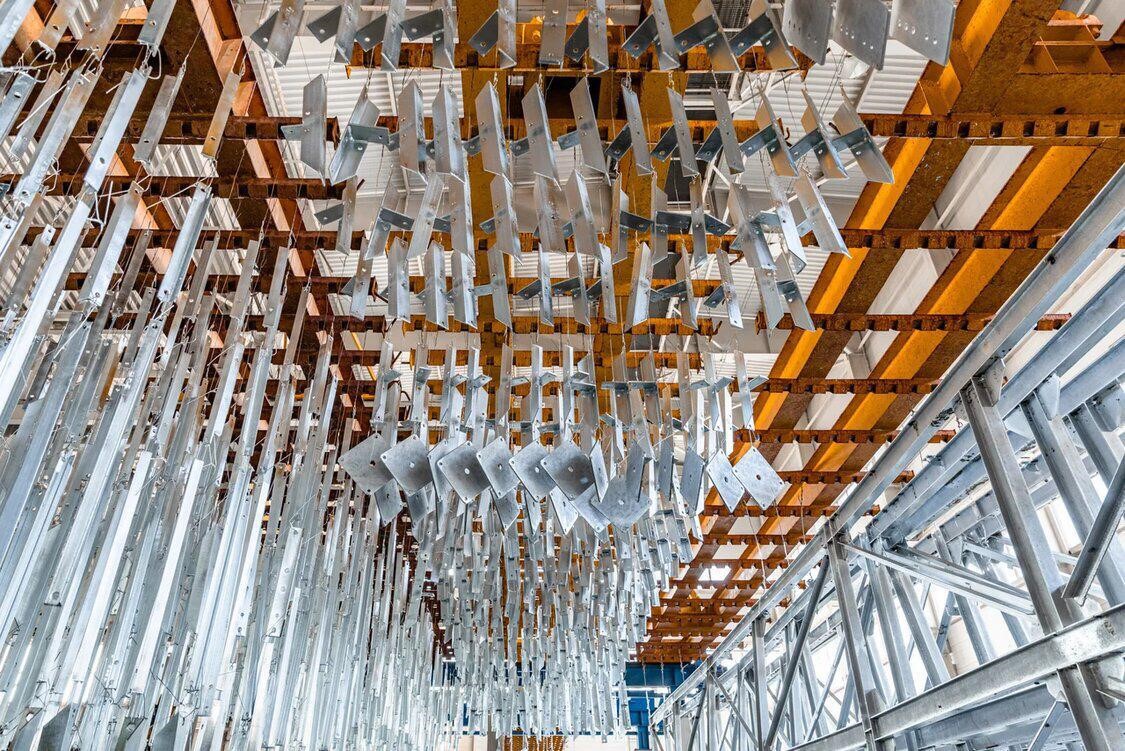
Помимо опор ЛЭП, «УМЕКОН» также производит опоры освещения, светофорные опоры, стойки жестких поперечин контактной сети для РЖД, каркасы жилых и промышленных зданий, башни радиорелейной связи, мостовые и дорожные ограждения, мачты освещения и т. д. Среди клиентов предприятия такие крупнейшие корпорации энергетического комплекса. Продукция завода успешно используется даже в регионах с суровым климатом, что говорит о ее высоком качестве.
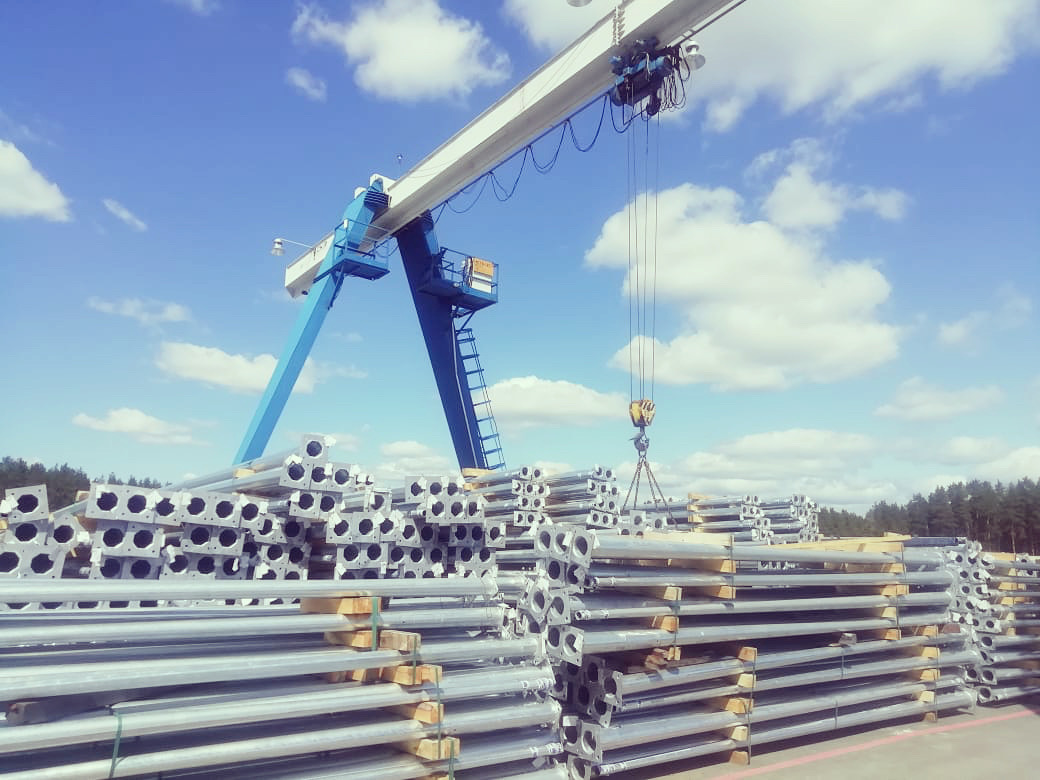
33 года во главе Уральского завода металлоконструкций находится Юрий Алексеевич Ставицкий. Свой трудовой путь на предприятии он начал главным инженером в 1987 году. А теперь Юрий Алексеевич с гордостью говорит о заводской династии Ставицких — вместе работают сыновья Константин, близнецы Дмитрий и Аркадий, внук Егор.
День рождения цеха горячего цинкования
18 июля 2013 года рядом с поселком Бобровский Сысертского района был произведен запуск цеха по оцинкованию металлоконструкций с применением новейших технологий. В тот день на торжественном открытии нового производства присутствовали представители руководства Свердловской области, главы Сысерти и Бобровского, зарубежные партнеры, руководители строительных компаний и многие другие. Почетным гостем мероприятия был старейший сотрудник завода Ян Аронович Песин, который трудится на предприятии с мая 1961 года.
Гостям праздника рассказали о важности горячего цинкования для экономики, объяснили, как происходит оцинковка, и даже показали сам процесс, выпустив на глазах у присутствующих первую продукцию.
Открытие цеха в Бобровском стало одной из причин экономического прорыва UMECON. За прошедшие 7 лет оцинковано более 270 тысяч тонн продукции.
Кроме того, появление нового цеха принесло ощутимую пользу экономике Сысертского городского округа — это и пополнение местной казны налогами, и новые рабочие места.
Современные технологии делают процесс оцинковки не только автоматическим, но и безопасным с точки зрения влияния на окружающую среду. Санитарная зона предприятия составляет не более 100 метров. Благодаря тому, что новый цех оснащен необходимым современным оборудованием, эффективность очистки газов, образующихся в процессе цинкования, составляет 99,9%.
К сожалению, на сегодняшний день на огромной территории России действует всего 20 подобных заводов горячего цинкования, тогда как в Европе их около 1000, в том числе 180 в Германии, 70 в Испании, 90 в Италии.
Технология горячего цинкования
Горячее цинкование позволяет защитить готовые металлоконструкции от различного вида коррозии, что в конечном итоге в несколько раз повышает долговечность изделий.
Перед нанесением слоя цинка конструкция проходит подготовительную обработку, которая включает в себя обезжиривание, травление, промывку и флюсование поверхности, чтобы ничто не помешало созданию прочной цинковой защиты. Затем изделие погружается в расплавленный цинк при температуре 450 °С. Рассмотрим этапы производства чуть подробнее.
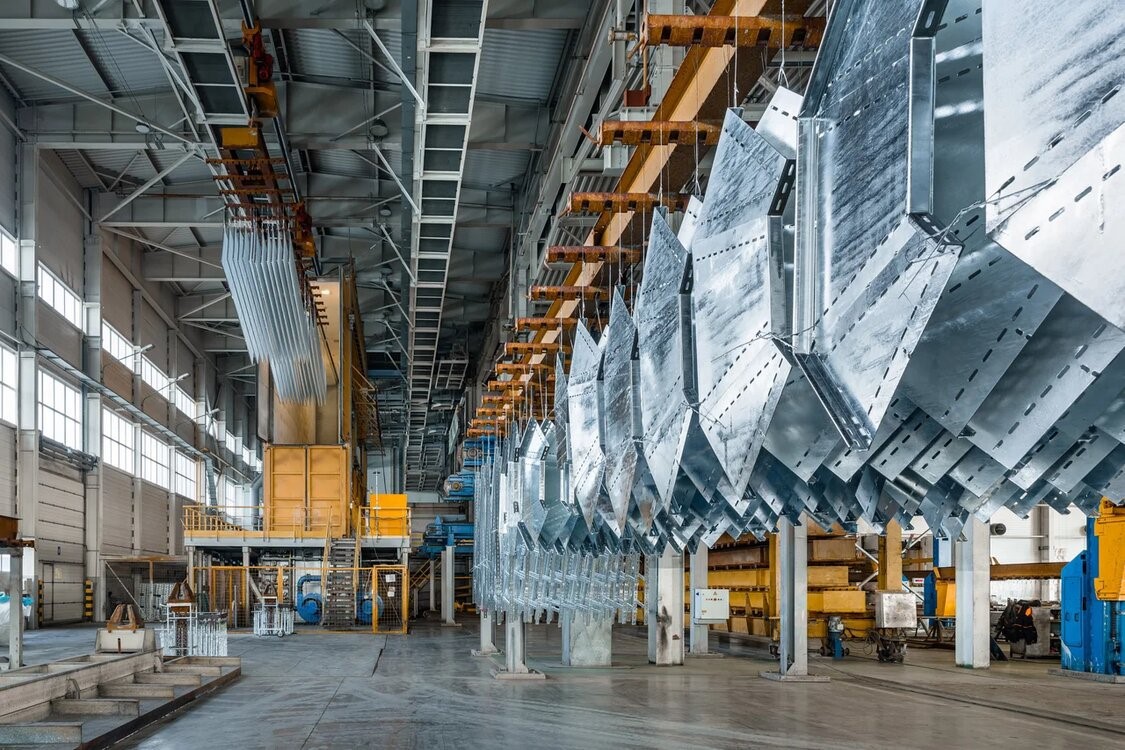
- Этап навески
Технологический процесс горячего цинкования полностью автоматизирован. Он начинается с поступления металлоконструкций в зоны навески с помощью двух однобалочных мостовых кранов. Далее с помощью подъемников производится навеска изделий на траверсы. Затем при помощи тележки загруженные траверсы передаются на оборудование блока зоны предварительной подготовки поверхности, где сразу включается соответствующая программа.
- Этап предварительной подготовки
В состав этого блока входит 13 ванн, которые состоят из химстойких полиэтиленовых вкладышей, поддерживаемых стальными конструкциями.
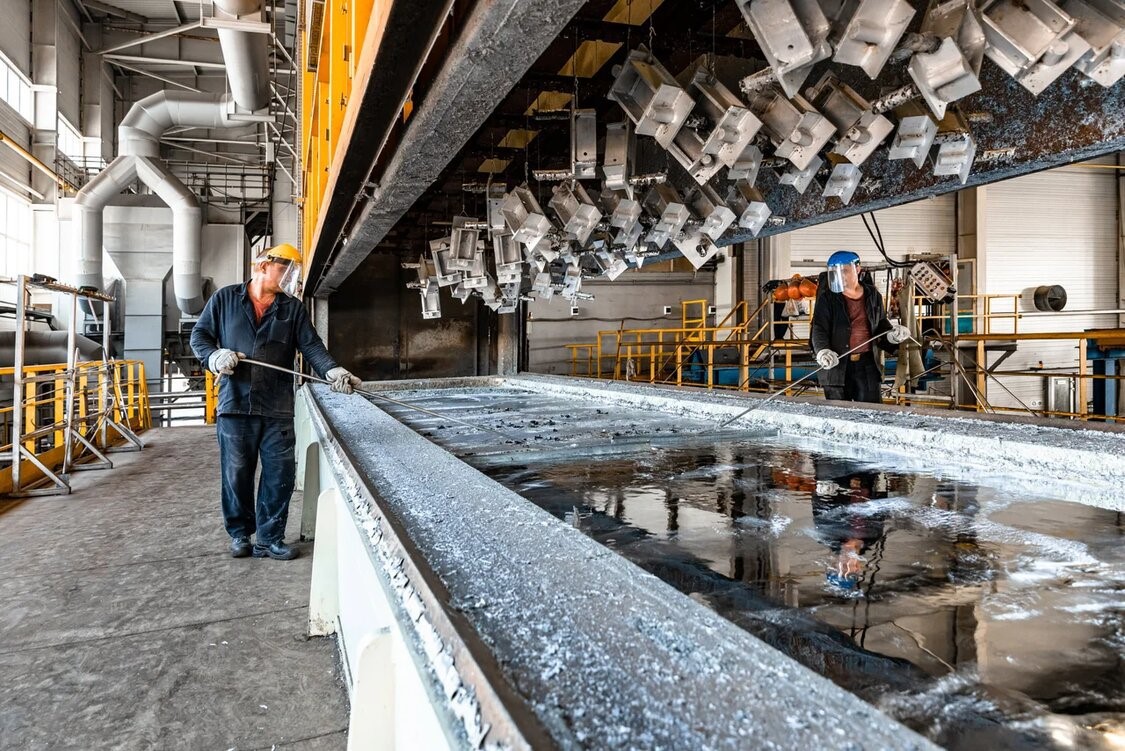
Предварительная подготовка осуществляется в четыре подэтапа:
- Обезжиривание. В ваннах обезжиривания снимаются масляные и другие загрязнения с поверхности металла, чтобы ускорить последующий процесс травления. Процесс обезжиривания выполняется путем погружения металлоконструкции в подогреваемый раствор на кислотной основе.
- Травление. В процессе травления снимаются все окислы с поверхности металла. Это необходимое условие для обеспечения диффузионного проникновения цинка в кристаллическую решетку железа, чем обеспечивается высокая стойкость цинкового покрытия.
- Промывка. После процесса травления необходимо смыть с поверхности металла остатки кислоты и загрязнений в ванных с водой, чтобы предотвратить их перенос в ванну флюсования.
- Флюсование. В ванне флюсования на изделие наносится флюсовая пленка, которая будет защищать его чистую поверхность от окисления под воздействием кислорода воздуха перед процессом оцинкования.
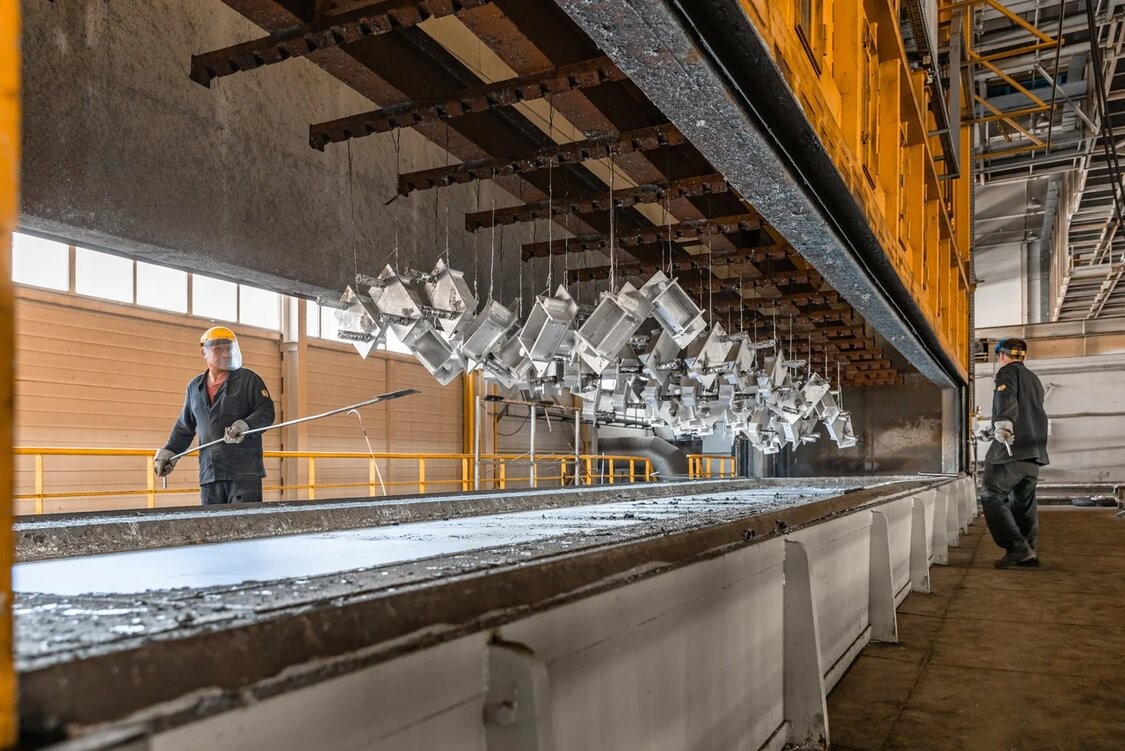
- Этап сушки
Перед погружением изделий в ванну с расплавленным цинком их подвергают сушке. В этом процессе осуществляется предварительный нагрев и удаляется излишняя влага с поверхности металла, что позволяет цинку меньше охлаждаться.
- Этап оцинкования
После сушки подвес с металлоконструкциями автоматически перемещается в зону оцинкования под защитно-вытяжной короб печи цинкования. Подготовленные детали с помощью тельферов опускаются в ванну с расплавленным цинком. Температурный режим расплава цинка должен поддерживаться на уровне 450 °С. Разогрев производится при помощи скоростных горелок, расположенных на торцевых стенках.
Ванна горячего цинкования закрыта со всех сторон защитно-вытяжным коробом, который предназначен для защиты персонала, а также улавливания белых дымов, образующихся в процессе обработки изделий. Отходящие от печи газы имеют высокую температуру. Их тепло не пропадает зря, оно используется для нагрева растворов в ванных предварительных обработок.
После окончания процесса оцинкования траверсы автоматически перемещаются на один из свободных транспортеров в зону снятия готовой продукции.
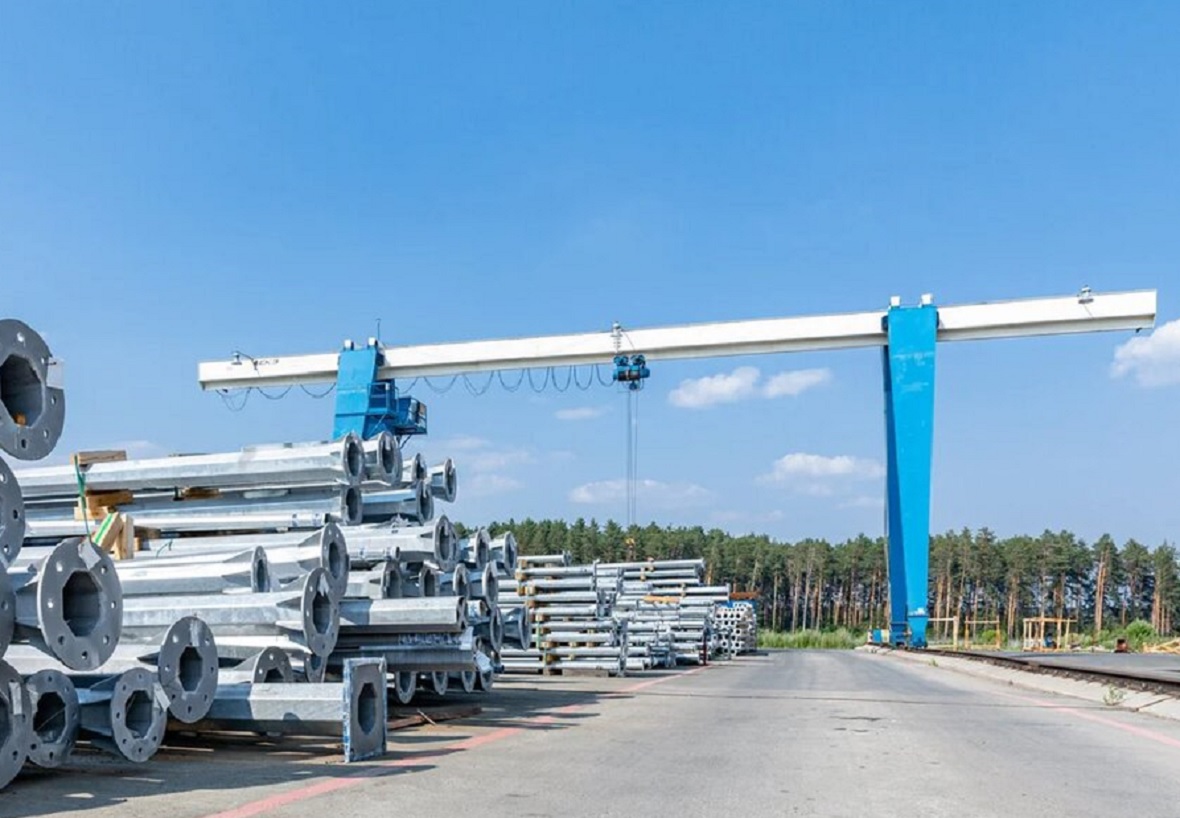
Благодаря применению современных технологий и наличию необходимых производственных мощностей UMECON лидирует в производстве металлоконструкций и опор ЛЭП на постсоветском пространстве, а также на высоком уровне выполняет срочные заказы. Завод достигает оперативности в том числе за счет хранения на своих складах неснижаемого запаса металлопроката для непрерывной работы в течение трех месяцев.