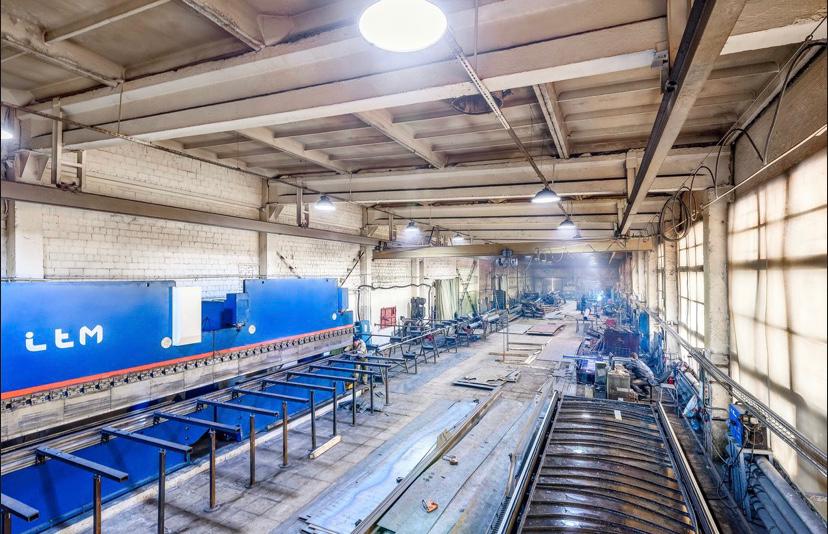
Идея
Впервые мысль о создании завода опор освещения ITM (Innovative technologies of metalworking) появилась в 2015 году. В то время мы уже производили светильники для промышленности и активно развивали направление по строительству линий уличного и дорожного освещения. Контракты по уличному освещению заключались с государственными заказчиками согласно условиям 44-ФЗ, а это высокое требование к качеству строительства и срокам исполнения.
Первые трудности успешного исполнения строительных контрактов возникли из-за «Поставщиков опор освещения». Мы вынуждены были закупать «чужие» опоры по высокой цене, порой низкого качества, и не вовремя. Как следствие, получали штрафы, пени по своим основным госконтрактам, ибо суров он, 44-й Федеральный Закон.
Скажу “спасибо” рынку производителей опор за трудности, которые стали толчком к осмыслению возможности производить все металлоконструкции для систем освещения своими силами!
Старт
Первые изделия для объектов строительства начали изготавливать в 2018 году. Это были закладные фундаменты для опор освещения (ЗДФ), производили мы их на той же площадке, где и светильники. Появились первые сварочные посты, сварные бригады. Начала формироваться команда инициативных производственников.
Для увеличения прибыли со строительных контрактов дополнительно начали производить кронштейны, купив первый б/у станок плазменной резки и трубогиб.
Следующим логическим шагом, чтобы полностью обеспечить наши строительные бригады всем необходимым, решили начать производство трубчатых опор. Для этого установили в цехе кран-балку, купили первый погрузчик по прозвищу «Митяй».
Вскоре смогли заключить субподрядные договоры по производству ЗДФ, кронштейнов и трубчатых опор с одним из крупных производителей. Заказ взяли по заниженной цене, но смогли отточить технологию производства, «набить руку».
В 2018 году выиграли торги на два крупных контракта по строительству освещения в Мурманской области и в городе Муравленко, ХМАО, где решили обеспечить строительство только собственными опорами. Попробовали найти партнера по гибке листового металла для изготовления обечаек (обечайка — конусовидная заготовка опоры), получили опыт по их варке и оцинкованию.
В режиме, когда на одной площадке располагалось два производства, мы проработали около полутора лет. Все это время мы наращивали объемы по производству закладных и кронштейнов. Начала выстраиваться структура внутри компании по данному направлению, сформировался отдел продаж.
Непредвиденные трудности
В конце 2018 года решили приобрести листогиб для изготовления граненых опор, начали прорабатывать детали покупки. Тщательно продумали основные характеристики пресса: усилие давления, размер зева, тандемный конструктив (два одинаковых пресса связанных между собой для увеличения длины рабочей поверхности). Нашли производителя станка в Китае и лизинговую компанию для покупки в рассрочку. Затем обратились в государственную структуру по поддержке производителей и направили заявку на покупку листогибочного пресса, потратив порядка 6 месяцев на подготовку документов, чтобы получить льготный кредит под 5%. Итог: нам отказали, программу закрыли.
В начале 2019 года, уже через коммерческий банк, получили одобрение по кредиту на покупку этого оборудования. Листогиб был заказан у производителя в Китае.
Летом 2019 года нам изготовили листогиб. Однако у нас все еще не было точного понимания, куда его ставить. Начали ездить по различным промышленным площадкам Екатеринбурга, искать новый цех, удобный для размещения «нашего тандемного пресса», большого стола плазменной резки, портала для сварки продольного шва и, конечно, наличие кран-балки с возможностью погрузки/разгрузки фур.
Нашли подходящее здание, которое состояло из двух помещений и казалось нам тогда огромным. Сломали стену — получился один большой цех.
С доставкой листогиба из Китая возникли очередные трудности. В собранном виде пресс являлся негабаритным, и, чтобы привезти его, пришлось бы потратить колоссальные деньги. Специально для нас его конструкцию сделали разборной. Готовый к отправке листогиб загрузили в два 40-футовых контейнера и так везли его из Китая.
Для сборки и настройки оборудования были привлечены специалисты из Китая. Сразу после их приезда начались сложности: во-первых, китайцы отказались есть местную пищу, и нам пришлось заказывать для них еду в ресторане китайской кухни; во-вторых, гости должны были пробыть у нас неделю, но им пришлось задержаться на три. Дело в том, что на следующий день после их приезда пришел первый контейнер с оборудованием, но оказалось, что в нем не один станок, а половина одного и половина второго. Собрать что-то из этого было невозможно. В результате долгих переговоров удалось убедить китайцев остаться дожидаться, когда придет второй контейнер, который тем временем где-то с Дальнего Востока двигался в нашу сторону. Но внутри контейнера произошло смещение груза, в результате чего была выбита его стенка. Поэтому груз был задержан таможней сроком на две недели. Из-за этого форс-мажора китайцы прожили у нас три недели. Мы развлекали их, как могли, когда была возможность выделить немного времени, вывозили гостей посмотреть город.
Наконец-то прибыл контейнер, закипела работа по сборке.
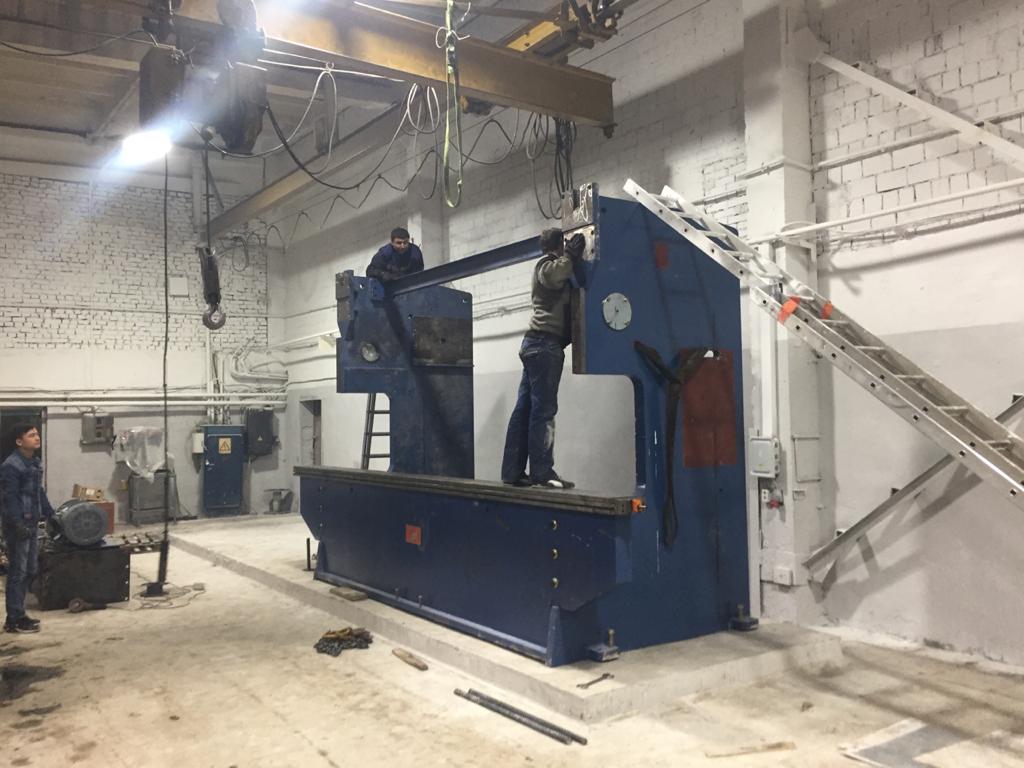
3 ноября 2019 года запустили листогиб, сделали первые заготовки. В ночь с 3 на 4 ноября китайцы улетели домой. А уже 11 ноября мы выпустили первую опору.
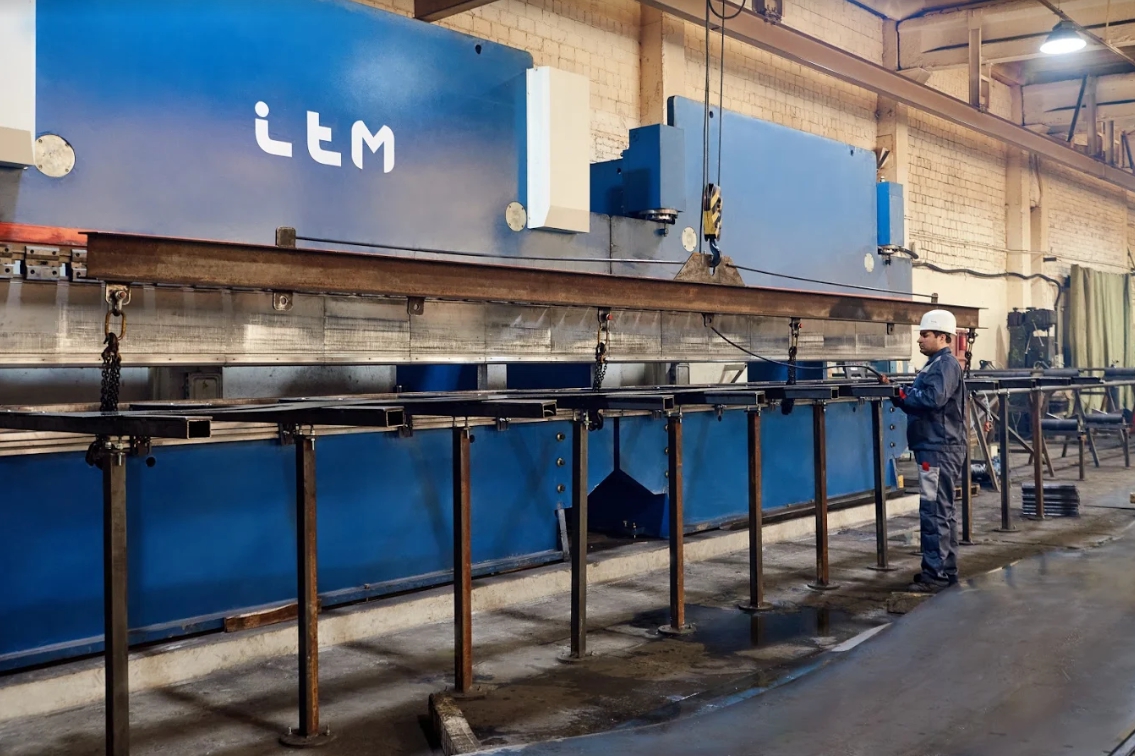
Сложности всегда были и будут — они не заканчиваются. Сложности с запуском оборудования, нехваткой людей, отладкой оборудования. Пока мы находимся на пути к своей максимальной производительности. Точки роста известны: оптимизация плазменного раскроя, собственное производство листа из рулона, мотивационная работа со сварщиками.
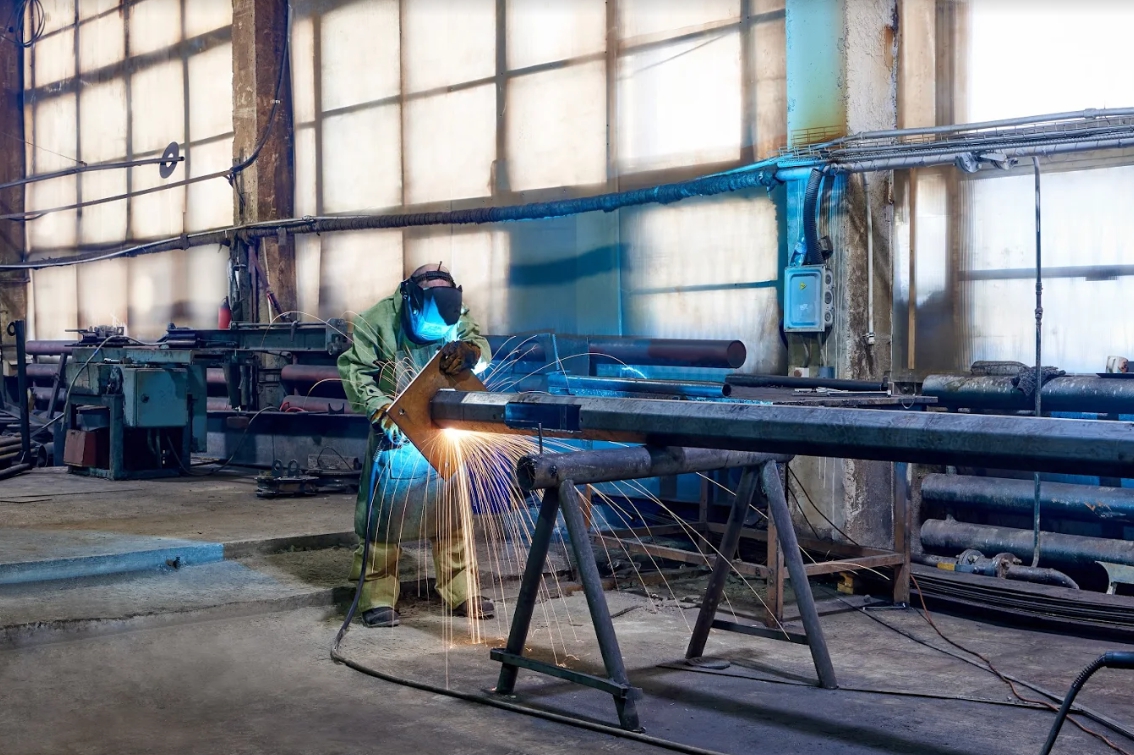
Пандемия COVID-19
Когда объявили первую неделю карантина, мы провели несколько совещаний, на которых было принято решение, что будем продолжать работать. Все понимали, что после таких денежных вливаний в запуск производства «денежной подушки безопасности» нет, и, если остановить работу завода, не будет возможности платить людям зарплаты. Практически все специалисты из бригад отнеслись к нашему объявлению с пониманием.
Компания получила официальное разрешение на работу. Обеспечили работников необходимыми средствами защиты (маски, антисептики). Ни дня наше производство не простояло в отличие от более крупных предприятий конкурентов. Это позволило взять ряд крупных заказов и загрузить производство. В эти месяцы пришлось экстренно расширяться. Запустили еще один цех по изготовлению трубчатых опор, установили в нем кран-балку, сварочные посты, вентиляцию, набрали еще порядка двадцати новых работников. На удивление окружающих, в то время, когда другие предприятия выгоняли людей в отпуска, мы на протяжении трех недель каждый день проводили по пять собеседований.
Итоги и планы
В первой половине 2020 года нам удалось осуществить полноценное раскрытие проекта ITM — на полную мощь заработал завод по производству опор освещения, компания расширила линейку выпускаемой продукции, произвели отладку станков, закупили транспорт для развития логистики.
Наша задача на 2020 год - повышение эффективности. Для нас это выдача большего количества изделий с высоким процентом качества тем же составом. Как только мы выйдем на плановую производительность, возобновим наш опыт по расширению станочного парка.
Целью на конец года является выпуск 40 единиц готовой продукции в смену.
На следующий год планируем отталкиваться от финансовых показателей. Планы амбициозные — хотим освоить 1 млрд рублей.
Подробнее на сайте
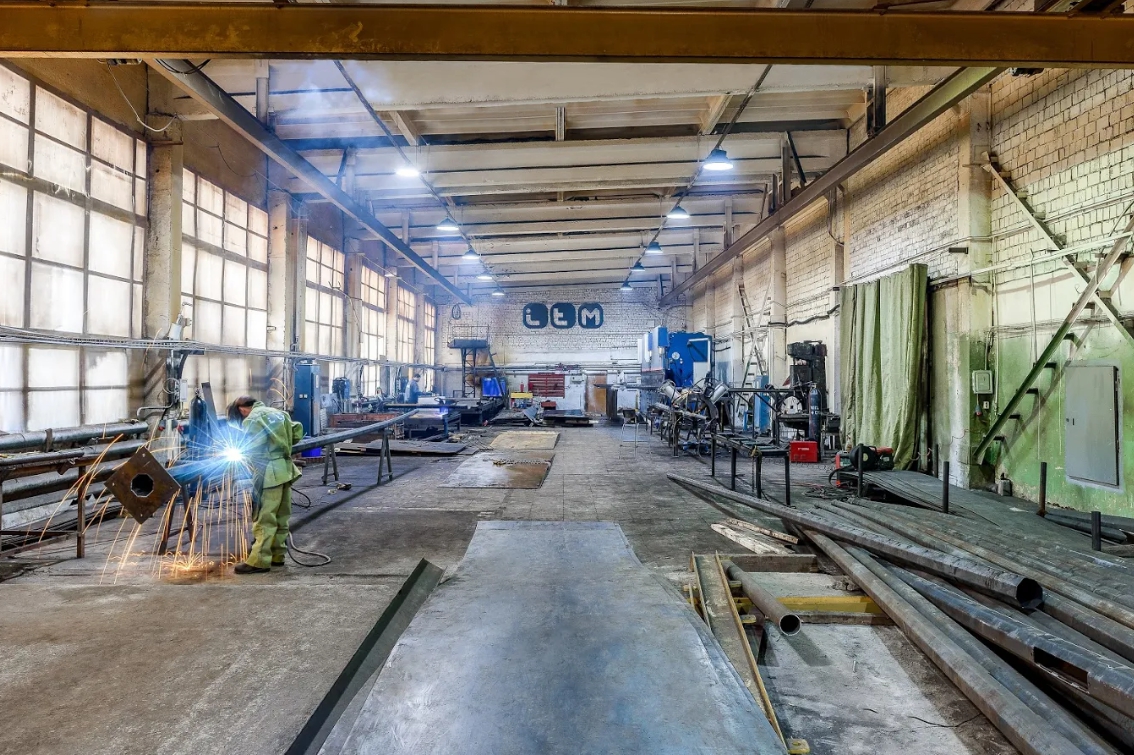